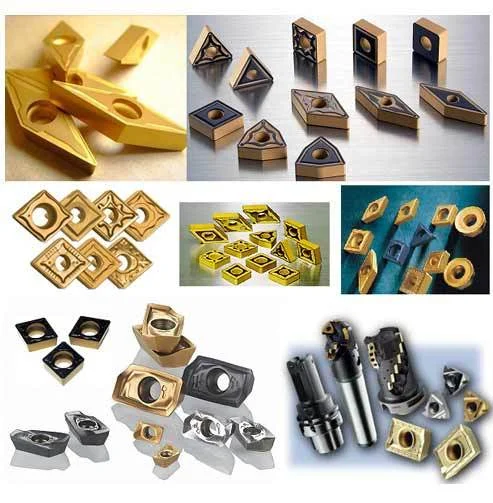
Uses of Carbide Inserts
A carbide insert is a tool used for accurately machining metal. Steel, carbon steel, cast iron, alloys at high temperatures, and non-ferrous metals with easy surface finishes can all be cut using this machine. You can easily replace the grips since many different types, sizes, shapes, and colors are available.
To keep your business running and competitive, it is essential to have the right equipment for metalworking. For different purposes, there’re different types of carbide inserts that are used. In the following article, you’ll find out all the applications of different kinds of inserts, including milling inserts, turning inserts, and aluminum inserts. Let’s dive in!
Types of Carbide Inserts
Carbide inserts are available in many types depending on your application requirements. Below is a list of some of the significant carbide inserts you are likely to encounter daily.
Turning Inserts
A turning tool body grips a replaceable insert attached to a lathe turret. Turning is typically done with a replaceable insert. Inserts for turning tools are manufactured using composite materials, coatings, and geometry features that provide high accuracy and high material removal rates.
Threading carbide inserts
The carbide insert thread mill is the term used to describe a piece of cutting insert that is used to create an internal or external thread within a part. These are typically attached to a tool holder on a lathe or a turning center, where they are usually used with tools.
In addition to thread mills and thread rolling, thread inserts are another method for creating threads on a workpiece similar to thread milling. Putting these replaceable commodities in their proper places as replacements wear out is essential.
Grooving carbide inserts
Based on the type of holder used, these inserts can cut grooves on both the outsides as well as the insides of a workpiece.
Among the many applications for which groove-making tools are relevant, there is a wide variety of hardware components of all types. These Carbide specialists specialize in determining the precise specifications required to suit the needs of each customer perfectly, regardless of whether they are parting off a smaller component or creating a deep groove with a large diameter. A Carbide insert can be grooved efficiently and expertly for extrusion grooving, internal grooving, face grooving, as well as parting. To maximize productivity and efficiency, you need to make sure that you choose the right tool. Every groove comes with its own set of challenges, no matter how wide or shallow it is. Additionally, every material used in the component’s manufacturing has its own properties and limitations. These three elements truly determine how the ideal tool should be designed, sized, and rated for the job.
Milling carbide inserts
The term milling insert refers to a piece of equipment that can be used to process materials such as steel and titanium without the fear of breaking the tool. The materials they help shape, they can straighten, shape, cut, and they can also cut metals such as steel, stainless steel, cast iron, non-ferrous materials, titanium, hardened steel, and plastic.
Drilling carbide inserts
With its high accuracy and high-performance indexable inserts, the Drilling and Hole Boring System is suitable for use on materials as diverse as aluminum and superalloys. With the drill body made of heat-treated steel that is very rigid, the nest for the insert is rigid and the flutes are straight, resulting in a long-term life for the insert and an efficient chip removal process.
Boring carbide inserts
Inserts made of cemented carbide are available in several sizes, shapes, and compositions that are used in various manufacturing methods on steels, cast iron, highly ferrous alloys, and nonferrous metals. In addition, machining metal parts more efficiently and with better finishes can be done when using carbide inserts. In addition to steel, stainless steel, hardened steel, cast iron, non-ferrous metals, titanium, and boring inserts are also good choices for applications.
How to choose the right insert
It would be best if you considered many factors to make the right choice regarding carbide inserts. Select insert geometry, insert grade, shape (nose angle), size, nose radius, and entry angle carefully to achieve reasonable chip control and machining performance.
- Choose insert geometry
A turning geometry can be divided into three basic types optimized for different operations: finishing, medium, and roughing.
Roughing
The combination of high feed rate and depth of cut results in an increased depth of cut. This is suitable for operations requiring the highest degree of edge security.
Medium
It includes operations that range from medium roughing to light roughing. You can choose something from a wide range of feed rates and depth of cut combinations.
Finishing
The combination of low feed rates and shallow depths of cut is ideal for shallow depths of cut. Applications that require low cutting force will benefit from this combination.
- Select the grade
Grades of inserts are selected primarily based on:
The ISO P, M, K, N, S, and H components
indicate the method (finishing, medium, roughing)
Manufacturing conditions (good, average, difficult)
- Choose an insert shape
I believe that you should choose the shape of the insert according to the amount of accessibility the tool requires at the point of entry. Selecting the smallest possible nose angle is recommended to provide insert strength and reliability. The margin for error has to be weighed against the variety of cuts made.
It requires more machine power and is more likely to vibrate more strongly when the nose angle is large. In addition to having a smaller nose angle, a minor cutting edge engagement can also make it more heat-sensitive as both of these things are weaker and more sensitive to heat.
Choosing a size
Adapting the insert size to the application’s requirements, as well as the space available for the cutting tool, should be considered.
The stability increases when the insert has a larger size. If you are going to be doing heavy machining, then the insert size should usually be over I.C. 25 mm (1 inch). In many cases, the size of a finished product can be reduced when it is finished.
Machining material
The purpose of carbide inserts is to enable the workpiece to be machined efficiently.
In this sense, it is of utmost importance to make sure that you choose the right tool for the purpose you have in mind. Several materials are available to us, including Aluminum, Bronze, Stainless steel, Cast Iron, and many others.
Types of carbide inserts for different Materials
Steel
Because the inserts are explicitly intended for use as inserts in steel surfacing operations. They can be run at faster clipping speeds and last longer than inserts used in various materials.
Cast Iron
The carbide insert for cast iron is made of abrasion-resistant carbide that will last longer, and then inserts are made of many different materials. Cast iron carbide inserts are made of an abrasion-resistant carbide, so their tool life is longer than inserts for other materials. Unlike the H series inserts, which can stick out from the holder to reach tight spaces on the workpiece with a negative rake, the K series inserts are the positive rake. Carbide inserts for cast inserts are commonly used for machining imperfectly round workpieces such as shafts with keyways since they were designed for semi-interrupted cutting conditions. You can install the inserts into the appropriate holder to begin using them.
Stainless Steel
Heat resistant and shaped for turning stainless steel specifically, these inserts will last longer than inserts for multiple materials.
Alloys
The inserts are not only heat-resistant and wear-resistant, but they also operate with outstanding performance when cutting super alloys such as titanium.
Multimaterial
With these premium turn-carbide inserts, your tool can cut a wide range of materials and is not required to change.
Non-ferrous Material
These premium inserts are ideal for cutting aluminum, copper brass, and other non-ferrous materials.
carbide Inserts
The performance of cutting tool materials has been continuously enhanced in response to users’ needs for higher cutting speed. The first high-speed steel appeared on the market in the beginning of the 1900s.
In the latter half of the 1970s, cemented carbide tools coated with alumina or titanium compound were developed and they enabled a far higher cutting speed. Meanwhile, cermet is a composite material consisting mainly of a hard titanium phase. Although cermet was originally developed for use as a jet engine material, it has evolved as a cutting tool material separately from other tool materials because of its low reactivity with steel and fine cutting surface.
Types of cemented carbide increased from four in the
1930s, S1 and S2 for steel and G1 and G2 for cast iron, to
26 in 1965.Cutting tool inserts are replaceable attachments for cutting tools that typically contain the actual cutting edge. And are effectively used in machining operations such as boring, construction, cut-off and parting, drilling, grooving, hobbing, milling, mining, sawing, shearing and cutting, tapping, threading, turning, brake rotor turning etc.
Features
Cutting tool inserts can have many different geometries. Round or circular inserts are used in mills or in radius groove turning. Like RCMX, RDKN, RNMG, RDKW etc.Three-sided inserts are triangle and trigon shapes are TPAN, TPKN, TPUN, TPGN, TNMG etc. Triangle inserts have a triangular shape and three equal sides with three tips and trigon insert is a three-cornered insert resembling a triangle, but with a modified triangular shape.Four-sided insert shapes include Rhombic. Like CNMG, CNMM, DNMG, DNMA etc Rhombic inserts are four-sided, with an angle on the y-sides for cutting point clearance.